Our R&D Journey
In my last blog post, “Operational Modal Analysis with DFAT”, I briefly shared an introduction to the groundbreaking work that MSI DFAT and Siemens DI SW pioneered in Modal Testing and Analysis. We were not just experimenting with unproven systems for the first time – actually, we are currently under contract to carry out the largest combined experimental and operational modal analysis with Direct Field Acoustic Testing (DFAT®) in the known history of experimental test engineering - one we hope to co-publish a paper on with our client soon. Pushing boundaries is nothing new for us; it’s a challenge we’ve taken on for over three decades.
This journey inspired me to delve into the exciting path MSI DFAT has taken in Research & Development, and the subsequent “proof in the pudding” that have helped establish our technology as the industry-leading gold standard. Since I've found great satisfaction in being part of our R&D efforts from the market research side (i.e., researching the true customer needs for vibroacoustic testing first-hand), I thought you might enjoy hearing about it too…
The Story About Research…
Every research project tells a story. The challenge, however, is that not all stories are worth reading. There are certainly “investigators” out there who craft their narratives first and then try to back them up with “research” (I’m thinking of various copycat companies who unsuccessfully attempt to replicate our proven DFAN testing systems and methods). But when it comes to head-to-head benchmark comparisons, we often find that these lackluster imitators can’t improve at all upon even the oldest innovations we’ve made decades ago (scroll to our timeline).
In the planning stages of research, it’s essential to harness energy to map out a path forward. A plan helps us gear up for the research, anticipate potential obstacles, and provides a framework to navigate uncertainty. There have been times when we began with over a hundred test cases, only to narrow them down to just ten before realizing we needed to change course entirely. For some, this shift might feel like a setback, but for us, it’s thrilling to be redirected from an initial idea to a more effective and adaptive solution.
Take, for instance, our very first forays into R&D for Direct Field Acoustic Noise (DFAN) testing. The first test we conducted with concert-type sound systems (line arrays) showed promise – but it was some incredibly expensive R&D! Our founder, Bob Goldstein, and Chief Engineer Paul Larkin, managed to blow up millions of dollars worth of line-array concert speakers during the initial DFAN tests. Ouch! They quickly realized that traditional concert speakers weren’t going to cut it for replicating launch conditions and shifted their focus to designing more powerful, compact, lightweight, simple-to-operate and structurally stable DFAT systems.
R&D didn’t stop there. We also sought out the brightest minds in test engineering globally, such as Dr. Marcos Underwood, “the godfather of MIMO testing”, to help pioneer advancements in Multi-Input, Multi-Output (MIMO) control methodologies. Today, using state-of-the-art MIMO noise control systems (NCS), we proudly say that our DFAT system is the only one in the world utilizing true narrowband MIMO control for precise response limiting. Other systems still rely on wide, and often risky, third-octave bands.
Another brilliant addition to our team is Wes Mayne. Wes helped MSI DFAT understand the key differences between traditional Reverberant Facility Acoustic Chamber Testing (RFAT) and Direct Field Acoustic Noise Testing (DFAT). Having designed RFAT facilities worldwide, Wes was instrumental in our understanding of the core benefits of DFAT over RFAT, and bringing the technology to the market.
Recently, a few unproven and risky startups have tried to enter the DFAT market, but they’ve largely failed thus far. With only a couple tests under their belt (one of which they only obtained almost by accident due to a small discrepancy in schedules) and a few very small system installations globally (mostly collecting dust while not even being actively used), we have so far been largely ignoring the noise. We had hoped the efforts of these companies would stoke the flames of healthy competition and help push the technology forward, ultimately benefiting the industry at large. After all, any improvements that help our customers further speed up testing, reduce costs, or lead to better results would be a win for us too—even if we weren’t directly involved. However, several long-term clients evaluated these new DFAT systems and concluded that the “new” speaker technology was vastly underwhelming.
The speakers? Paraphrasing the voice of our customers: too bulky and heavy to fit in many Assembly Integration & Test (AI&T) facilities. For example, one system that was installed butted directly against a shaker table, leaving barely enough clearance - mere inches - from the speaker-face to the Unit Under Test (UUT) (reference the redacted image below). Acoustic measurements from such a poorly designed test setup would lead to contaminated results, if not outright failure for operators and equipment to effectively navigate within the tight test volume. The test levels? Their loudspeakers couldn’t match the required acoustic spectra needed for clients’ testing specifications. The technology? Despite a couple new patents on box designs, it showed no real improvements over the DFAT systems already available.
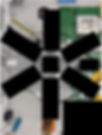
This led me to ask a crucial question: Why are we even paying attention at all to alternative DFAN testing systems, and not trying to incrementally improve our own even more - for the sake of science and for our customers?
Development vs. Diversion
At this point, an old friend reached out with a surprisingly relevant question: “If you had to design a system for DFAT, how would you do it?” While I wasn’t the only one consulted, I immediately understood the weight of the question. I quickly shared a few observations from my recent experiences with customer engagements, and specifically the following, based on their commentary:
Make the system compact, while still much more powerful than necessary (a comment I viewed as a jab at the bulky and oversized nature of other DFAN systems)
Ensure the system is easy to set up, but not so simple that it loses its modularity or the ability to be tailored for specific tests (a comment I viewed as a playful reference to other DFAN systems that try to stuff all the frequency ranges into one super heavy and hard-to-move box)
Guarantee that the setup is structurally stable and able to remain perfectly level as vertical height increases, to avoid tip-over risk to our spacecraft (something only our systems can do!)
This valuable feedback prompted MSI DFAT to design a completely new loudspeaker unit, adding even more capability to our repertoire. While we can’t share any details about this new design yet, it is already being used for contracted DFATs in 2025.
Learning From Mistakes
While new DFAN companies are bound to make many careless mistakes, we’ve long since learned to avoid almost every imaginable issue from a DFAN test. For example, new, unproven companies will likely place microphone arrays in the least optimal positions, or promise to meet acoustic testing specifications their unproven systems can’t possibly reach - just to gain a new client for some quick, short-term revenue.
Fortunately, MSI DFAT owns our design and production process, giving us the ability to make nearly instant changes solely for the benefit of our customers. Because of this flexibility, and our long-term mindset with R&D at the forefront, we continue to be the trusted partner in modern acoustic testing for the aerospace industry.